Wybór filamentu do produkcji obudowy
W części drugiej tego cyklu omówione zostały parametry najróżniejszych filamentów. Przypomnijmy sobie kilka z nich za pomocą tabeli 1. Wybrano do niej materiały potencjalnie najlepiej nadające się do wykonywania obudów, ale przy założeniu, że chcemy mieć możliwość druku na każdej, nawet relatywnie taniej drukarce 3D. Obudowa powinna być wytrzymała zarówno mechanicznie, jak i termicznie. Już na początku widać, że nie są to cechy najpopularniejszego materiału „drukarskiego”, czyli PLA. Szczególnie wytrzymałość w poprzek warstw jest dość niska, a to implikuje też niską wytrzymałość na siły ścinające. Jeśli wydrukujemy wewnątrz obudowy elementy montażowe do radiatora lub innego, cięższego elementu, to mogą one z łatwością się oderwać przy uderzeniu z boku. Wytrzymałość termiczna też jest na tyle mała, że obudowa zdeformuje się od stania na blacie, w snopie światła słonecznego w ciepły dzień. Ponadto PLA pod długotrwałym obciążeniem powoli się deformuje.
Materiałem wyglądającym najlepiej pod względem mechanicznym jest PCTG. Filament ten jest niemal tak samo wytrzymały w poprzek warstw, co wzdłuż warstw, zaś pod kątem wytrzymałości termicznej jest lepszy od PLA i porównywalny do PETG. Jego główną wadę stanowi mała popularność. Cenowo tworzywo to wypada porównywalnie do dobrej klasy PLA czy PETG. Kolejnym kandydatem na materiał obudowy jest ASA – filament, który stanowi „podkręconą” wersję ABS. Pod względem mechanicznym okazuje się niewiele lepszy od PLA, ale ma wyższą temperaturę topnienia. Z ABS wykonuje się wiele najróżniejszych produktów, w tym właśnie obudowy, więc pokrewny mu ASA powinien być dobrym wyborem. I byłby, gdyby nie dwa dość poważne problemy: wysoka temperatura druku i duży potencjał do deformowania się. ASA nie za bardzo nadaje się do drukowania dużych paneli i choć teoretycznie można drukować go na wolnym powietrzu, to warto mieć drukarkę wyposażoną w komorę i to najlepiej ogrzewaną. Z drugiej strony, jeśli mamy już ową komorę, a sama drukarka może osiągnąć zalecane temperatury druku, jest to najlepszy wybór na obudowy do elektroniki.
Ostatnimi dwoma filamentami w tym podstawowym zestawieniu są PETG i PET. Oba materiały mają zbliżone właściwości, są łatwo dostępne i relatywnie tanie. PET oferuje wyższą temperaturę mięknięcia i większą wytrzymałość, ale wynika to z jego wyższej elastyczności. Obudowa wykonana z opisywanego materiału wymaga uwzględnienia tego problemu, a – co za tym idzie – dodania elementów i profili zwiększających sztywność, jak na przykład żebra czy wkładki z innych, wytrzymalszych materiałów. PETG jest materiałem sztywniejszym, przez co mniej wytrzymałym mechanicznie i termicznie. Przy odpowiednim rozmieszczeniu komponentów w projekcie i użyciu aktywnego chłodzenia żaden element obudowy nie osiągnie temperatury 80°C. Podobnie przy wystawieniu na działanie słońca urządzenie nie nagrzeje się aż tak bardzo. PETG to dobry materiał do prototypowania, ma jednak drobny problem: bardzo dobrze przylega do powierzchni blatu. Na tyle dobrze, że blat należy smarować zwykłym klejem w sztyfcie, który pełni funkcję bufora między wydrukiem a powierzchnią. Takie rozwiązanie umożliwia bezproblemowe drukowanie dużych paneli.
Warto nadmienić, że właściwości wszystkich tych materiałów można poprawić przez wyżarzanie. Zmienia ono strukturę materiału, poprawiając zarówno własności termiczne, jak i mechaniczne. Dlatego obudowy z ABS wykonane metodą wtryskową są znacznie wytrzymalsze od tych drukowanych. Niestety wielkim problemem związanym z tą metodą postprocessingu jest zmiana wymiarów, a często też i kształtu tak potraktowanego wydruku. Najlepszym sposobem na zachowanie wymiarów jest zatopienie wydruków w wysokiej klasy gipsie przeznaczonym do wykonywania form dla protez dentystycznych i aparatów ortodontycznych. Proces jest kłopotliwy, zajmuje dużo czasu i wymaga poniesienia dodatkowych kosztów, jednak nie zawsze gwarantuje dobre rezultaty. Być może metoda ta zostanie szerzej opisana w przyszłości jako ciekawostka. Teraz natomiast przejdźmy do kolejnego etapu pracy nad obudową.
Model bryły urządzenia z podziałem na panele oraz elementy wewnętrznej konstrukcji
Obudowa urządzenia będzie składać się z siedmiu paneli: podstawy, ścian bocznych, ścianki tylnej oraz przedniej, panelu kontrolnego (umocowanego pod kątem) oraz pokrywy górnej. W ten sposób każdy panel może być wydrukowany powierzchnią zewnętrzną do blatu, co znacząco zwiększy też wytrzymałość całości. Na tym etapie należy też rozważyć, które panele będą trwale związane ze sobą, a które powinny być demontowalne. Nic nie stoi na przeszkodzie by cała obudowa była rozbieralna, ale niekoniecznie musimy używać w tym celu wtapianych wkładek gwintowanych oraz ukazywać wszystkie wkręty. Dlatego wybór padł na użycie ukrytych nakrętek w panelu dolnym i tylnym. W podobny sposób umocowane zostaną też elementy wewnątrz obudowy. Panel przedni, sterujący i pokrywa będą mocowane za pomocą wtapianych wkładek gwintowanych. Przy użyciu tych samych wkładek umocowana zostanie płytka panelu kontrolnego. Wymiary obudowy to 112×112×180 mm. Rysunek 1 prezentuje ogólną formę obudowy.
Dolny panel funkcjonuje jako główny element nośny ciężaru całego urządzenia. Do niego właśnie przymocowane zostaną panele boczne i tylny, a także radiator o wymiarach 125×72×35 mm oraz elementy związane z aktywnym chłodzeniem. Dlatego już na tym etapie należy uwzględnić montaż tych elementów. Panel będzie miał grubość 2 mm ze wzmocnieniami o grubości 4 mm, pod nimi właśnie ukryte będą nakrętki M2,5. W trakcie procesu drukowania należy pamiętać o wstrzymaniu druku na czas montażu tych nakrętek. Rysunek 2a pokazuje plan panelu, a rysunek 2b – gotowy element.
Kolejnym podzespołem jest panel tylny, zaprezentowany na rysunku 3. Jego szkic powstał jednak jako ostatni, by zagwarantować dobre spasowanie całości. Użyto w tym celu płaszczyzny konstrukcyjnej, odsuniętej od frontowej części panelu przedniego na 180 mm. Płaszczyzny takie, w różnych wariantach, pozwalają łatwo stworzyć nawet dość skomplikowane kształty. W tym jednak przypadku szkic na płaszczyźnie konstrukcyjnej pozwala nam na dodanie otworów w panelach bocznych, gdyż panel tylny jest do nich przykręcany dzięki wtapianym wkładkom. Same wkładki mocują też do niego panel górny. Dwa wkręty M2,5×6 łączą omawiany element z panelem dolnym. Aby zrealizować opisane założenia projektowe, utworzono dodatkowy szkic pomocniczy. Jedynym istotnym detalem tego panelu jest otwór na gniazdo IEC-C14, wokół którego znajduje się wzmacniające zgrubienie.
Dwa panele boczne są częściowymi odbiciami lustrzanymi – zachowują ten sam kształt i wzmocnienia, ale panel lewy (rysunek 4) ma miejsce na wentylator 80×80 mm oraz zasilacz modułowy 12 V/3 A. Na etapie prototypowania zadbano też o ładne i estetyczne wykonanie kratki wentylacyjnej – forma otworów podąża za kierunkiem obrotów wentylatora i profilem łopatek.
Panel prawy (rysunek 5) został utworzony za pomocą płaszczyzny konstrukcyjnej, odnoszącej się do boku panelu dolnego. W dolnej części ma on otwory wlotowe, nachylone pod kątem 60°, co odpowiada nachyleniu panelu kontrolnego. Tutaj też znajdują się dodatkowe wzmocnienia i kolejne zatopione nakrętki M2,5 – tym razem do zamocowania elementu wzmacniającego konstrukcję, który ogranicza przy okazji kierunek przepływu powietrza i przytrzymuje radiator od góry. Oba panele mają wtopione wkładki gwintowane, do których przykręcone będą: panel przedni, kontrolny i górny. Dzięki temu serwisowanie urządzenia i wymiana najbardziej narażonych na uszkodzenia paneli będzie prosta. Ze względu na duże rozmiary komponentów i niewielką objętość obudowy, upakowanie wszystkiego wymagało pewnej dozy wyobraźni. Elementy, zwłaszcza te znajdujące się na lewym panelu bocznym, są spasowane na styk, a wentylator może potrzebować dodatkowego zaokrąglenia jednego z narożników. Pewną pomocą byłaby wizualizacja wszystkich komponentów, ale nie jest to konieczność – tak długo, jak pamiętamy o krytycznych wymiarach. Dla drobnego ułatwienia szkice paneli zawierają też linie konstrukcyjne wizualizujące sam radiator.
Panel górny, przedni i kontrolny zostały „wyciągnięte” ze szkicu panelu lewego. Do wewnętrznych powierzchni tych elementów przypisane zostaną szkice, które pozwolą dodać nie tylko wszystkie otwory montażowe, ale też wzmocnienia i otwory do montażu gniazd, przycisków czy włącznika zasilania. Łby wkrętów trzymających te panele będą wystawać nad powierzchnię urządzenia i jest to celowy zabieg estetyczny. Również panel tylny jest w ten sam sposób umocowany, ale w tym wypadku zostało to podyktowane względami technicznymi – panel nie może być zbyt gruby. Przy okazji stajemy przed wyborem: możemy użyć w tym miejscu wkładek wtapianych niskich lub wysokich. Wkładki M2,5 wymagają otworu o średnicy 3,2 mm i głębokości, zależnie od wariantu, 3 lub 5 mm. Wybór padł na wkładki 3 mm, gdyż wzmocnienia, w których będą mocowane, mają grubość tylko 6 mm. Do skręcenia obudowy użyte będą wkręty walcowe M2,5×6 mm. Wysokość łba tych tego typu wkrętów wynosi maksymalnie 2,5 mm, a średnica – 4,5 mm (ma to znaczenie przy projektowaniu otworów w panelach bocznych i innych elementach). Na razie jednak zajmijmy się panelem górnym, który poza otworami ma też odpowiednie wzmocnienia – pokazują to rysunki 6a (szkic) i 6b (gotowy panel, widok od spodu). Panelem przednim i kontrolnym zajmiemy się później.
Obudowie brakuje jeszcze dwóch elementów montażowych do zainstalowania radiatora i elementu ograniczającego ruch powietrza. Przy okazji można też wykonać dodatkowy element pozwalający łatwiej ustalić położenie otworów montażowych dla płytki drukowanej układu – ta będzie dokręcona do radiatora na elementach dystansowych.
Osłona radiatora została wykonana na kolejnej płaszczyźnie konstrukcyjnej, tym razem odnoszącej się do panelu prawego. Kształt jest dość skomplikowany – zastosowanie fazowania nie tylko wzmacnia całość, ale pozwala też wydrukować ten element bez użycia wsporników, jeśli się go odpowiednio ustawi. Rysunek 7a pokazuje sam element, a rysunek 7b prezentuje go w połączeniu z panelami, do których jest umocowany.
Rysunek 8 obrazuje elementy montażowe radiatora oraz przymiar dla płytki drukowanej. Elementy montażowe będą mocowane wkrętami M2,5×8 do panelu dolnego i wkrętami M4 do radiatora. Zapewnia to wystarczającą sztywność całości, zwłaszcza przy uwzględnieniu elementu dociskowego, jakim jest osłona radiatora. Przymiar zaś zaprojektowany został tak, by dało się go z łatwością nałożyć na radiator o szerokości 125 mm i wywiercić oraz nagwintować wszystkie potrzebne otwory – z wyjątkiem tych, które trzymają komponenty chłodzone radiatorem (te zostaną wykonane w trakcie składania urządzenia).
Panel przedni i kontrolny
Jak wspomniano wcześniej, panele te są „wyciągnięte” ze szkicu panelu lewego. Panel przedni ma wbudowany włącznik zasilania, przełącznik gniazd oraz cztery gniazda bananowe o rozstawie 19×19 mm. Wyznaczono też otwór pod gniazdo TRS 3,5 mm, ale jest on zaślepiony cienką warstwą plastiku, gdyż stanowi opcjonalne wyprowadzenie portu UART. Panel ma dodatkowe wzmocnienia usztywniające, zwłaszcza w okolicach gniazd bananowych – model gotowego elementu pokazano na rysunku 9.
Szkic panelu kontrolnego (rysunek 10) jest najbardziej skomplikowanym szkicem w całym projekcie. Należało odtworzyć nie tylko kształt i wymiary płytki, ale też wymiary i położenie przycisków, enkodera, diod LED i całego wyświetlacza LCD. Dla wyświetlacza narysowano nawet wymiary pola znaków, by następnie użyć narzędzia odstępu, by wykonać właściwy kształt otworu w panelu. Wielu autorów projektów amatorskich popełnia błąd, wycinając otwór pod wyświetlacz wielkości metalowej ramki, która mocuje matrycę do płytki drukowanej. Jest to nad wyraz nieestetyczne, gdyż powoduje „uciekanie” światła z wbudowanego podświetlenia wokół ramki, a dodatkowo w ogóle nie chroni wnętrza obudowy. Co ciekawe, ten sam błąd projektowy można spotkać w chińskich produktach opartych na amatorskich projektach. Dlatego też w naszym przypadku otwór pod wyświetlacz jest tylko o 3 mm większy od pola znakowego, a dla poprawy widoczności jego krawędzie zostały dodatkowo sfazowane. W ten sposób nie tylko chronimy wnętrze urządzenia – a zwłaszcza płytkę panelu kontrolnego – ale także zapobiegamy „wyciekowi” światła i mało estetycznemu wyglądowi ekranu – jego dioda pozostaje całkowicie ukryta. Ten sam sposób postępowania można, a wręcz należy stosować także do wyświetlaczy graficznych. Od spodniej strony wyświetlacza znajduje się też wzmocnienie otaczające metalową ramkę, w nim znajdują się również odpowiednie otwory montażowe. Wysokość tego wzmocnienia, a zatem i innych elementów panelu, zależy mocno od grubości ramki, a ta – od grubości podświetlacza. Standardowe wysokości ramek to 7,5 mm i 8,6 mm. W tym wypadku zastosowany zostanie wyświetlacz wyższy, o odwróconych kolorach.
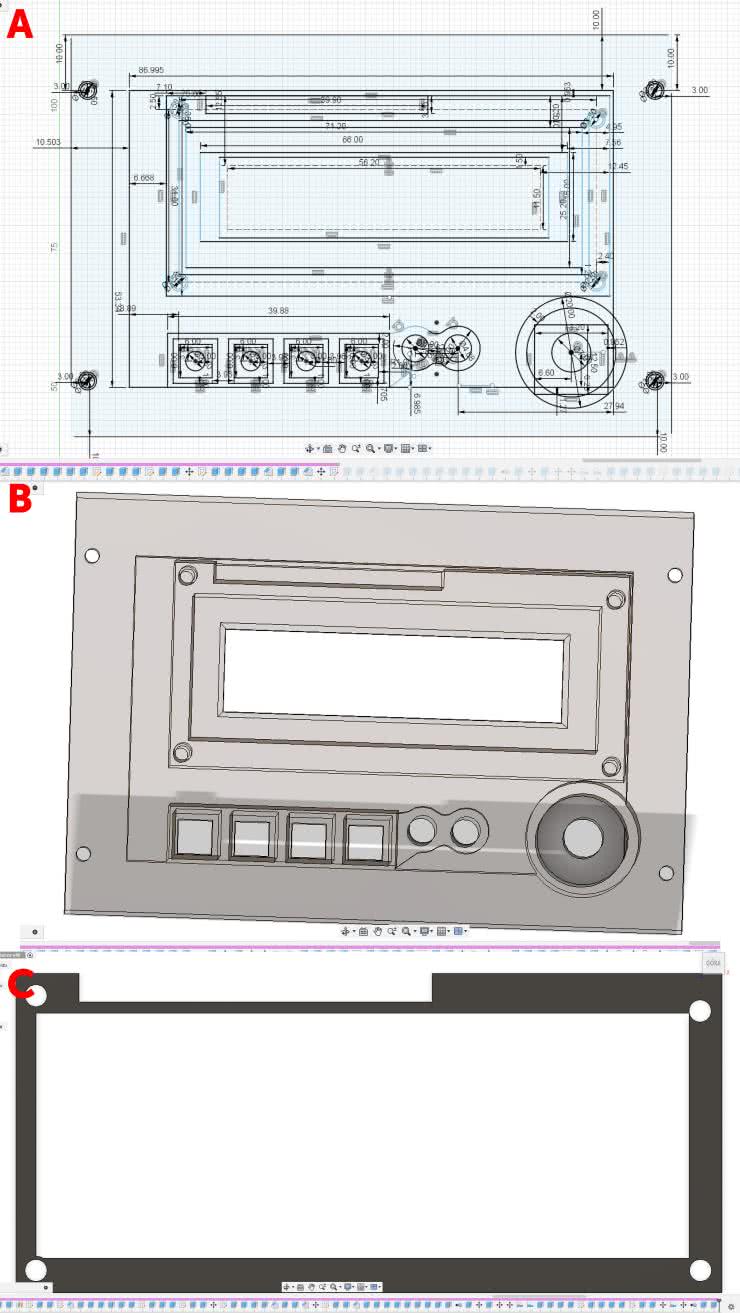
Wokół diod LED również dodano wzmocnienie o wysokości 5 mm, przez co diody będą tylko nieznacznie wystawać nad powierzchnię panelu. Same otwory są nieco mniejszej średnicy, by diody nie miały nadmiernych luzów montażowych. Wokół otworów na przyciski znajdują się kolejne wzmocnienia, ale ich głównym przeznaczeniem jest stabilizacja klawiszy, które będą nałożone na mikroprzełączniki. Dla enkodera dołożono „niszę”, by móc go przykręcić do panelu, a – co za tym idzie – dodatkowo wzmocnić całość. Na bazie tego samego szkicu wykonano również element dystansowy do umieszczenia między wyświetlaczem a właściwą płytką drukowaną sterownika.
Rysunek 10a prezentuje szkic panelu od przodu, a rysunek 10b – gotowy panel. Przekładka z rysunku 11 pasuje do każdego wyświetlacza LCD 16×2 i zalecam Czytelnikom korzystanie z takiego właśnie rozwiązania. Ostatnimi elementami do wykonania są klawisze i gałka. Te pierwsze są dość prostymi blokami tworzywa z otworem z jednej strony (na umieszczenie trzpienia mikroprzełącznika), z drugiej zaś znajdują się wgłębienia w formie liter V, C, M oraz E. Tu objawia się największa wada programu Fusion 360: tworzenie tekstu i jego pozycjonowanie stanowi nieliche wyzwanie, gdyż narzędzie do tworzenia napisów jest nieintuicyjne i nie ma podstawowych funkcji. Dość powiedzieć, że próbując zmienić położenie litery, można przypadkiem zmienić jej rozmiar i ją obrócić. Użytkownicy od lat zgłaszają problemy z tym narzędziem, a firma Autodesk... od lat konsekwentnie je ignoruje.
Gałka jest znacznie wyższa, niż pierwotnie planowano, ze względu na dość długą osi enkodera – ta wystaje na 13,6 mm ponad panel. Dlatego też sama gałka musi być odpowiednio grubsza. Dla poprawienia estetyki jej kształt jest też nieco bardziej skomplikowany, z wcięciami na palce i skośnymi bokami. Gałkę i klawisze można obejrzeć na rysunku 11.
Zakończenie
Rysunek 12 pokazuje gotowy projekt obudowy. Nie jest ona jednak w stu procentach kompletna, brakuje jej kilku napisów, ale te zostaną dodane, gdy projekt urządzenia będzie już ukończony.
W następnej części wydrukujemy obudowę (z uwzględnieniem ukrytych nakrętek), wtopimy w nią wkładki i zamontujemy komponenty. Zabierzemy się też za zastosowanie druku 3D do konstrukcji z elementami mechanicznymi. Technologia wytwarzania przyrostowego okazuje się niezwykle użyteczna przy budowie takich komponentów, jak części maszyn i robotów, nietypowe formy sensorów czy obudowy inne niż proste pudełka.
Paweł Kowalczyk, EP