Przemysł półprzewodnikowy już niejednokrotnie przyczynił się do rewolucji w różnych dziedzinach życia i pracy, zastępując drogie i dopracowane technologie, nowymi, mniejszymi, tańszymi i lepszymi alternatywami. Tego typu rewolucja jest teraz możliwa właśnie w zakresie monitorowania łańcucha chłodniczego, poprzez zastąpienie dotychczasowych, aktywnych systemów monitorowania, niedrogimi, małymi tagami RFID, wyposażonymi w sensory.
Czy da się stworzyć lepsze rozwiązanie?
Aktualnie istniejące systemy logistyczne, pozwalające na sprawne monitorowanie łatwo psujących się dóbr powstawały przez lata i kosztowały miliardy dolarów. Nowe RFID z sensorami, współpracujące czytnikami kosztującymi kilkadziesiąt dolarów mogą sprawić, że dotychczasowe rozwiązania staną się przestarzałe.
Oczywiście duże korporacje są w stanie inwestować w złożone systemy monitoringu, które łączą w sobie podsystemy śledzenia pozycji w czasie rzeczywistym, zaawansowane oprogramowanie, aktywne znaczniki pracujące na częstotliwościach radiowych, układy komunikacji bezprzewodowej i pobieranie danych z satelitów GPS, nawet pomimo ogromnych kosztów i konieczności ciągłej konserwacji.
Łączne koszty posiadania takich systemów obejmują także abonamenty na przesył danych przez sieci komórkowe, utrzymywanie oprogramowania, wyposażenie wszystkich kontenerów i ciężarówek w odpowiednie urządzenia oraz wyposażenie każdej lokalizacji, w której znajdują się kontenery w bezprzewodowe punkty dostępu do transmisji danych.
Systemy te dostarczają informacji, które pozwalają natychmiastowo reagować na wszelkiego rodzaju usterki układów chłodzenia. I pomimo że wydawałoby się, że tego typu instalacje są w stanie całkowicie wyeliminować wszelkie straty łatwo psujących się dóbr, w praktyce nie gwarantują 100-procentowej skuteczności.
Często okazuje się np., że diagnozowanie przyczyn problemu przeciąga się. Natomiast rozwiązania zapasowe, takie jak zastępcze kontenery chłodnicze lub zespoły pracujące w terenie, umożliwiające szybkie przechwycenie zagrożonych towarów są bardzo kosztowne w utrzymaniu i nie zawsze działają tak, jak powinny. Mimo to, aktualnie istniejące systemy działają właśnie w oparciu o takie mechanizmy, gdyż w czasie gdy powstawały, nie było lepszych rozwiązań.
Nowe technologie pozwalają jednak zastosować zupełnie inne podejście do kwestii ochrony towarów szybko psujących się. Poprzez wykorzystanie odpowiednich znaczników RFID, umieszczanych bezpośrednio na pojedynczych opakowaniach zbiorczych, można całkiem skutecznie chronić posiadane dobra, bez ponoszenia kosztów wielkich systemów.
Co prawda, systemy oparte o RFID nie zapewniają możliwości ciągłego monitorowania lokalizacji poszczególnych dóbr, co w praktyce będzie niekiedy prowadzić do pewnego zwiększenia strat towaru, ale wystarczy porównać koszty wdrożenia jednego lub drugiego rodzaju systemu, by przekonać się, że nowe podejście jest opłacalne.
Tanie monitorowanie
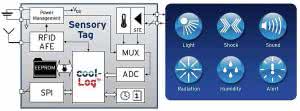
Rysunek 2. Znacznik obsługujący czujniki pracuje tak, jak konwencjonalny tag RFID, ale dodatkowo ma wbudowany sensor temperatury i może komunikować się z zewnętrznymi czujnikami
Koncepcja taniego monitorowania towarów w logistyce, opartego o niedrogie, jednorazowe znaczniki RFID, kosztujące kilka centów za sztukę jest dobrze znana w przemyśle. Pasywne znaczniki RFID mogą być odczytywane przez prosty czytnik RFID - komunikacja realizowana jest poprzez wysłanie sygnału radiowego z czytnika, który następnie jest odpowiednio rozpraszany przez znacznik. Dzięki temu sam tag nie wymaga własnego zasilania, korzysta z energii odbieranego sygnału radiowego i teoretycznie może pracować nieskończenie długo.
Konwencjonalne, pasywne znaczniki RFID zawierają małą ilość nieulotnej pamięci, w której zapisany jest unikalny kod identyfikacyjny. Wyobraźmy sobie jednak, co by było, gdyby znacznik wyposażyć dodatkowo w funkcję rejestrowania danych. Dałoby się wtedy tworzyć nowe tagi RFID, które mogłyby komunikować się z czujnikami. Zapisywałyby np. informacje o temperaturze, wibracjach i wilgotności, na jakie narażony był pakunek (rysunek 1).
Ponieważ omawiane znaczniki korzystałyby z istniejącej technologii RFID, ich odczyt opierałby się o znane i sprawdzone mechanizmy, dzięki czemu byłby łatwy do implementacji przez firmy. Wbudowując w tag sensor temperatury i pamięć EEPROM do zapisu danych oraz interfejs do komunikacji z zewnętrznymi czujnikami, charakteryzujący się małym poborem energii, możliwe staje się monitorowanie warunków środowiskowych dla każdego opakowania zbiorczego indywidualnie (rysunek 2).
Aktualnie stosowane technologie pozwalają na monitorowanie warunków na poziomie całego kontenera - np. poprzez pomiar temperatury wewnątrz ciężarówki lub w magazynie. Natomiast system oparty o małe znaczniki jest w stanie działać znacznie bardziej precyzyjnie, bo w odniesieniu do pojedynczych opakowań zbiorczych - najczęściej kartonów.
Oznacza to, że tak zaprojektowany system nie tylko jest tańszy w instalacji i użytku, ale też bardziej dokładny. To bardzo dobry przykład sytuacji, w której dzięki przemysłowi półprzewodnikowemu można zrewolucjonizować określoną dziedzinę przemysłu, podnosząc jakość działania, przy jednoczesnym obniżeniu kosztów.
Dwa tryby pracy
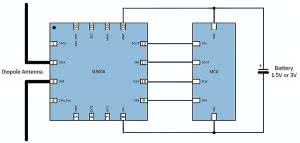
Rysunek 3. Podłączenie mikrokontrolera do znacznika RFID za pomocą interfejsu SPI pozwala znacznie zwiększyć możliwości takiego układu w odniesieniu do monitorowania łańcucha chłodniczego
Znaczniki wyposażone w sensory mogą być wykorzystane na dwa sposoby. Pierwszy najbardziej przypomina użycie konwencjonalnych pasywnych RFID. Sam znacznik nie ma wtedy własnego źródła zasilania, co zarazem oznacza, że nie ma wbudowanego zegara czasu rzeczywistego ani kalendarza.
Gdy jest skanowany, wybudza się i pobiera typowo 4 mA prądu z odbieranego pola elektromagnetycznego. Z tych 4 mA, jedynie 150 µA wystarczy do obsłużenia interfejsu zewnętrznego sensora i wbudowanego czujnika temperatury (rysunek 2).
Oznacza to, że zapisywanie danych zbieranych z czujników odbywa się tylko wtedy, gdy następuje skanowanie opakowania. Czas również pobierany jest ze skanera drogą radiową i wraz z odczytanymi danymi, po zaszyfrowaniu zapisywany jest we wbudowanej pamięci. Dzięki temu zanotowany komunikat jest zarazem chroniony przed niepowołanym dostępem.
Alternatywą jest użycie znacznika z wbudowaną baterią. Może on pracować w trybie półpasywnym, gdzie dzięki małemu źródłu energii może samodzielnie decydować o momentach odczytu danych. Jednocześnie podtrzymywany jest zegar czasu rzeczywistego (z ew. kalendarzem), który dostarcza informacji o aktualnym czasie, potrzebnych do określania momentów wybudzenia i do uzupełniania wskazań o znaczniki czasu. Typowe baterie stosowane w znacznikach tego typu wystarczają na rok do półtora roku pracy, przy czym okres ten zależy silnie od interwału pomiędzy kolejnymi rejestracjami danych i od rodzaju użytej baterii.
Wybór znaczników z sensorami
Omawiane, nowoczesne znaczniki RFID oferuje firma AMS. Aktualnie dostępne są dwa rodzaje tagów, odpowiadających potrzebom monitorowania łańcuchów chłodniczych w logistyce. Oba zawierają wbudowane czujniki temperatury, pozwalające na wykonywanie pomiarów w zakresie od -40°C do +125°C.
Model SL13A pracuje na częstotliwości 13,56 MHz i jest zgodny ze standardami ISO15693 i NDC-V. Model SL900A korzysta natomiast z pasma UHF, a więc częstotliwości z zakresu 860...960 MHz, zgodnie z wymaganiami EPC Gen 2 Class 1 i Class 3. Oba wspierają polecenia cool-Log.
Najprostszy przykład użycia tych podzespołów to rejestrowanie temperatury i identyfikacja w trybie w pełni pasywnym, a wiec w obecności czytnika RFID. W tym celu należy użyć standardowych komend do identyfikacji pojedynczego znacznika oraz specjalnej komendy "Get Sensor Value", wchodzącej w skład poleceń cool-Log.
Jeśli znacznik ma rejestrować dane również wtedy, gdy w pobliżu nie ma czytnika, konieczne jest zastosowanie baterii. Układy SL13A i SL900A można wyposażyć w baterie o napięciu 1,5 V lub 3 V. Jeśli użyta bateria jest płaska, cienka i elastyczna, możliwe jest wykonanie transpondera również na elastycznym podłożu. To najtańsza postać, umożliwiająca tworzenie niedrogich, jednorazowych znaczników. Jeśli tag ma być wielokrotnego użytku, zaleca się użycie małej baterii płaskiej i podłoża w postaci płytki drukowanej.
W przypadku gdy znacznik ma korzystać z baterii do rejestrowania danych z czujników, należy używać klasycznych komend RFID do identyfikacji tagu oraz komend cool-Log, takich jak:
- "Set Log Mode",
- "Initialise",
- "Start Logging",
- "Stop Logging".
Interfejs SPI
Zarówno układ SL13A, jak i SL900A obsługują interfejs SPI (Serial Peripheral Interface) do łączenia się z zewnętrznymi urządzeniami, takimi jak np. mikrokontrolery (rysunek 3). Dzięki temu możliwe jest zwiększenie zakresu funkcji realizowanych przez znacznik wspierany mikrokontrolerem.
Oprócz rejestrowania danych z czujników i identyfikacji opakowań możliwe jest m.in. łączenie się z modułem komunikacji przez sieć komórkową, co pozwala na bezpośredni zdalny dostęp do zapisanych informacji. Mikrokontroler pozwala też łatwo ustawiać rejestry znacznika oraz uruchamiać jego funkcje.
Jednostka obliczeniowa może przykładowo być zaprogramowana do alarmowania o wystąpieniu niepożądanych warunków czy też do obliczania przewidywanego czasu, przez jaki dany produkt będzie jeszcze przydatny do użycia lub spożycia.
Interfejs SPI może posłużyć nie tylko do odczytu i zapisu wbudowanej pamięci EEPROM, ale też jako narzędzie do testowania i kalibracji oraz wpisywania własnego kodu i identyfikatorów, co pozwoli na wykorzystywanie niestandardowych protokołów radiowych.
Podsumowanie
Znaczniki AMS SL13A i SL900A, dzięki obsłudze czujników pozwalają na zautomatyzowane monitorowanie i zapisywanie informacji o łańcuchu chłodniczym, takich jak temperatura, ciśnienie, wilgotność i wibracje. Poprzez zaawansowane funkcje mogą posłużyć do wywoływania alarmów lub przesyłania powiadomień, gdy warunki panujące w otoczeniu przekraczają zadane granice.
W efekcie pozwala to na realizowanie systemów opartych o zdarzenia, a więc znacznie prostszych niż aktywne monitorowanie kontenerów. Co więcej, nowe podejście jest tańszą alternatywą, a jednocześnie cechuje się dużą dokładnością. Spełnia wszelkie wymagania nowoczesnego przemysłu.
Shawn Rezaei
Inżynier aplikacyjny
AMS
www.ams.com