Niewielkie wiertarki zasilane prądem stałym to niezbędne wyposażenie warsztatu każdego elektronika i majsterkowicza. Przeważnie mają one jedynie wyłącznik zasilania, a do precyzyjnych zadań często potrzeba czegoś więcej. Postanowiłem samodzielnie wykonać możliwie najbardziej "wypasiony" sterownik, mający wszystkie funkcje, które przyszły mi do głowy oraz dodatki, jakich mi dotychczas brakowało przy pracy z wiertarką.
Schemat urządzenia pokazano na rysunku 1. Napięcie zasilania jest doprowadzane do PAD1-PAD2 - na schemacie oznaczone je etykietą VCC. W obwodzie zasilania włączono kondensatory filtrujące oraz diodę zabezpieczającą (transil). Rozdzielono masy - dla elektroniki sterującej (GND1) oraz sekcji wyjściowej (GND2).
Do zasilania elektroniki cyfrowej jest wymagane napięcie +5 V, które jest stabilizowane przez przetwornicę obniżającą z układem IC1 (MCP16301), pracującej w typowej konfiguracji aplikacyjnej. Zastosowanie diody Schottky (D6) zamiast prostowniczej zmniejsza straty energii (niższe napięcie progowe i brak zjawiska reverse recovery). Przed sekcją zasilającą włączono bezpiecznik polimerowy o prądzie znamionowym 750 mA.
W obwodzie jest dużo kondensatorów filtrujących zasilanie - rozmieściłem je w pobliżu doprowadzeń zasilających układy scalone oraz w ważnych miejscach. Głównym komponentem sterownika jest mikrokontroler ATmega16A, w którym wykorzystano praktycznie wszystkie zasoby sprzętowe. Jest on taktowany za pomocą rezonatora kwarcowego 16 MHz. Obwody analogowe mikrokontrolera są zasilane przez fi ltr LC, napięcie to jest jednocześnie wartością odniesienia dla wbudowanego przetwornika A/C. Zastosowano również układ generujący sygnał zerowania DS1813-10, zapewniający poprawny start po uruchomieniu zasilania oraz wstrzymujący pracę IC10, gdy napięcie zasilania spadnie poniżej 4,35 V - kontrola tego napięcia jest bardzo ważna, aby zapobiec ryzyku uszkodzenia danych w pamięci EEPROM. Do mikrokontrolera dołączono pozostałe bloki urządzenia.
Jednym z najważniejszych jest obwód drivera mocy sterującym zasilaniem silnika wiertarki. Wykonano go z użyciem tranzystora MOSFET-P (Q8) i sterowanego przebiegiem PWM. Dioda D9 bocznikuje zawartą w strukturze tranzystora diodę antyrównoległą, która łatwo (razem z całym tranzystorem) może ulec uszkodzeniu. Tranzystor włącza zasilanie silnika dołączanego pomiędzy PAD13-PAD14. Szybka dioda D10 eliminuje przepięcia powstające przy wyłączaniu klucza Q8. Napięcie odkładające się na R53 pozwala na obliczenie natężenia prądu pobieranego z wyjścia. Tranzystor Q8 jest sterowany przez driver TC4431 (Microchip) z wejściem TTL. Układ ma dwa wyjścia - jedno (OUT1) zasilające i drugie (OUT2) rozładowujące pojemność bramki tranzystora. Maksymalne napięcie bramka-źródło nie może przekroczyć ±20 V, aby nie uszkodzić tranzystora IRF9530. Zabezpieczeniem jest 15-woltowa dioda Zenera D8, która może ulec uszkodzeniu, gdy będzie aktywne wyjście OUT2 (silnik włączony). Wtedy prąd ograniczają rezystory R46 i R47. Logiczny sygnał sterujący z mikrokontrolera jest doprowadzony do linii MOTOR-PWM.
Jako generator PWM pracuje Timer1. Rezystor- zwora R45 normalnie nie jest montowany chyba, że zamierzamy pracować przy napięciu VCC mniejszym od 7 V. Na wszelki wypadek pozostawiono dla niego miejsce na płytce drukowanej.
Pomiar prądu wyjściowego odbywa się za pośrednictwem szeregowego opornika pomiarowego R53 (0,1 V). Różnica napięcia pomiędzy jego wyprowadzeniami jest wzmacniana po wcześniejszym fi ltrowaniu dolnoprzepustowym (fD=17 Hz). Filtrowanie jest to konieczne, ponieważ występują tętnienia (z przebiegu PWM), a mierzymy wartość średnią. Aktywnym elementem wzmacniającym sygnał jest wzmacniacz nieodwracający zbudowany w oparciu o połówkę układu LM358. Postanowiłem tak dobrać parametry, aby po kwantowaniu i pomiarze w przetworniku A/C mikrokontrolera, każdy kwant odpowiadał 5 mA prądu. Wzmocnienie jest regulowane za pomocą potencjometru R56 i powinno ono wynosić ok. 9,76 V/V. Kondensator C45 w pętli ujemnego sprzężenia zwrotnego stanowi zwarcie dla wysokich częstotliwości i zapobiega wzbudzeniu się wzmacniacza. Sygnał wyjściowy trafi a na wejście przetwornika A/C mikrokontrolera (linia MOTOR-MEAS). Rezystor R52 oraz duodioda D7 stanowią zabezpieczenie. Obie masy - GND1 i GND2 - są połączone w jednym punkcie, blisko padów zasilających, na schemacie oznaczonym J1.
Wykaz elementówModuł z mikrokontrolerem Rezystory: Kondensatory: Półprzewodniki: Inne: |
Jednym z założeń było wsparcie dla przycisków nożnych skokowych (zwykłe przełączniki monostabilne) oraz płynnych (odmiana potencjometrów), przeznaczonych do urządzeń muzycznych. Zastosowano je ze względu na łatwą dostępność. Są one standardowo zakończone wtykiem Jack 6,3 mm mono (skokowy) lub stereo (płynny). O ile budowa skokowego pedału i połączeń do wtyczki mono są oczywiste, warto jednak powiedzieć coś o muzycznych pedałach płynnych, czyli ekspresji lub głośności. Tego typu urządzenia mają wbudowane potencjometry i trzy wyprowadzenia. Standardowo, do styku tip wtyczki jest dołączony ślizgacz. Do styku sleeve jest podłączony ClockWise, a do ring CCW. Dla nas jest ważne, aby ślizgacz był na tipie, do pozostałych dostosujemy się programowo. Pedały tego typu mają rezystancję z zakresu 5...500 kV (ekspresji - małą, gitarowe głośności - dużą).
Zalecam stosowanie raczej tych o mniejszej rezystancji.
Urządzenie automatycznie rozpoznaje typ współpracującego z nim pedału. Gniazdo dołączamy do 4-pinowego JP1 - na schemacie ideowym są narysowane połączenia do wtyczki. Na wszelki wypadek zastosowano bezpiecznik polimerowy F1. Mikrokontroler sprawdza poziom logiczny na linii FOOT-PLUG, na której występuje "1", jeśli w gnieździe nie ma wtyczki, a zero, jeśli włączono wtyk. Rezystor R1 pełni podwójną funkcję - razem z C5 tworzy filtr dolnoprzepustowy usuwający zaburzenia zewnętrzne, a poza tym wraz z duodiodą D2 zabezpiecza port mikrokontrolera przed przepięciami.
Rezystor R2 ustalają poziom logiczny przy rozwarciu styków. Takie same filtry i zabezpieczenia włączono na każdej linii zewnętrznej.
Po podłączeniu wtyczki, w czego następstwie jest zerowana linia FOOT-PLUG), układ odczekuje ok. sekundę, aż wsuniemy wtyczkę do końca i ustalą się napięcia. Następnie przetwornik A/C mikrokontrolera mierzy napięcie na linii FOOT-TYP. Jeśli dołączyliśmy pedał skokowy (wtyczka mono), będą zwarte piny 1 i 3, więc zostanie zmierzone napięcie bliskie +5 V. Dodatkowo, zakładając, że w momencie dołączenia pedał był zwolniony jest wyznaczana jego polaryzacja (NO lub NC - później można zmienić). Wtedy też jest ustawiana linia FOOT-STER2, co włączy tranzystor i dołączy rezystor pull-down do linii FOOT-MEAS. Nie może on być dołączony na stałe, bo przy zastosowaniu pedału głośności o dużej impedancji, będzie on praktycznie zwarciem do masy. Do określenia pozycji pedału nie jest sprawdzany poziom logiczny na FOOT-MEAS, lecz jest mierzone napięcie i porównywane z połową zakresu napięcia występującego pomiędzy masą a dzielnikiem R3/R5.
W sytuacji, kiedy przyłączymy pedał płynnej regulacji, będzie on rezystancją włączoną między piny 1-3 tworząc z R6 dzielnik napięcia. Wówczas na FOOT-TYP będzie napięcie z zakresu od 0,4 V (500 kV) do 4,5 V (5 kV) i na tej podstawie mikrokontroler typ pedału. Jeśli napięcię będzie niższe, oprogramowanie uzna to za błąd i nie umożliwi wykorzystania tego manipulatora. Po uznaniu pedału za możliwy do użycia, jest ustawiana linia FOOT-STER poszerzając zakres napięcia wyjściowego. Rezystancja R7 (220 V) praktycznie nie wpływa na zakres pomiarowy, ale ogranicza prąd w przypadku zwarcia lub błędu, jak również przez krótką chwilę podczas wyciągania wtyczki, kiedy to zwierane są ze sobą 1 i 3, co zapobiegnie reakcji bezpiecznika polimerowego F1 (mają ograniczoną liczbę cykli).
Ładowane są z pamięci EEPROM dane kalibracji i polaryzacji, a gdy ich brak - wartości domyślne. Podobnie jak w przypadku pedału skokowego, również i tutaj pozycja jest wyznaczana na podstawie napięcia na FOOT-MEAS.
Kolejnym blokiem są dwukolorowe wyświetlacze 7-segmentowe. Użytkownik może wybrać wyświetlaną na nich treść oraz kolor świecenia (stały lub uzależnić go od wybranego parametru). Dla potrzeb realizacji tej funkcji brakowało dostępnych wyprowadzeń mikrokontrolera, więc zastosowałem rejestry przesuwne z zatrzaskiem (IC3, IC4 - 74HC595) dołączone do interfejsu SPI. Wyjścia 74HC595 są 3-stanowe, co przydaje się do wyłączania wyświetlaczy. Jak wspomniałem, wyświetlacze są dwukolorowe. Mają po dwie anody, osobno dla każdej barwy świecenia. W moim układzie kolor może być regulowany płynnie przez mikrokontroler, z wykorzystaniem przebiegu PWM (kanał B timer1), wyprowadzonego na linię 7SEG-RG (zero-zielony, jedynka- -czerwony), anody są włączane przez klucze na tranzystorach PNP Anoda czerwona jest zasilana z niższego napięcia (3,3 V), po to, aby wyrównać jasność świecenia obu kolorów. Niższe napięcie wytwarza stabilizator IC2 typu 78L33.
Sterownik wiertarki mierzy i wyświetla napięcie zasilania. Służy do tego dzielnik R8/R10. Kondensator C11 usuwa składowe o dużej częstotliwości. Duodioda zabezpiecza wejście mikrokontrolera. Pomiar napięcia odbywa się na linii SUPPLY- -MEAS. Odczytaną wartość należy przemnożyć przez 6. Jest to przydatne, ponieważ łatwo można stwierdzić, kiedy przeciążamy zasilacz.
W sterowniku zastosowano impulsator zintegrowany z przyciskiem. Aby ułatwić obsługę impulsatora, zastosowałem sprzętowe filtrowanie ewentualnych drgań jego styków z użyciem buforów z przerzutnikiem Schmitta (IC6, IC8) oraz obwodów RC. Rezystory R44 i R50 ograniczają prąd rozładowania oraz zapobiegają powstawaniu zaburzeń elektromagnetycznych. Wyjścia buforów IMP-A i IMP-B są kierowane do mikrokontrolera. IMP-B jest doprowadzony do wejścia wyzwalania przerwania INT0, skonfigurowanego na zbocze narastające. Kiedy ono wystąpi, jest sprawdzany stan IMP-A i na tej podstawie określany kierunek obrotów. Dla wygody, wyprowadziłem pady do programowania ISP mikrokontrolera oraz wszystkie napięcia zasilające i masę. Rezystor-zwora R41 ma być montowany po zaprogramowaniu, aby odłączyć na czas tego procesu układ resetujący.
Źródło prądowe (15 mA) do zasilania diod LED oświetlających miejsce pracy zbudowano z użyciem drugiej połówki LM358 (IC9B). Bezpiecznik F3 zabezpiecza przed skutkami zwarcia. Podświetlenie dołączamy do JP2. Maksymalna liczba połączonych szeregowo diod LED zależy od napięcia zasilającego. Można przyjąć, że suma spadków napięcia na diodach nie powinna przekroczyć VCC-1,5 V.
Montaż
Sterownik wiertarki zmontowano na dwustronnej płytce drukowanej, której schemat montażowy pokazano na rysunku 2. Jej kształt i rozmieszczenie otworów zostały dostosowane do obudowy Z19, a wolna przestrzeń w prawym dolnym rogu to miejsce na złącza przykręcane do panelu bocznego. Montaż rozpoczynamy od układów scalonych SMD. Następnie montujemy niskie elementy bierne, diody, bezpieczniki polimerowe, tranzystory. Nie montujemy rezystora- zwory R46. Potencjometry montażowe zostawiamy na później, aby ich nie zabrudzić topnikiem. Montujemy dławik L1 i kondensatory elektrolityczne oraz dokładnie sprawdzamy poprawność montażu. Lutujemy elementy przewlekane - zaczynamy od najniższych (rezystory, diody, dławik L2, rezonator kwarcowy z podkładką silikonową, podstawki dla wyświetlaczy LCD i 7-segmentowych. Muszą one znaleźć się na odpowiedniej wysokości, przy górnej pokrywie obudowy.
Dla wyświetlaczy LED zastosowałem rozcięte podstawki precyzyjne pod układy scalone. Montaż podstawki i wyświetlacza LCD jest trochę bardziej skomplikowany. Między płytką sterownika a płytką wyświetlacza musi być odstęp ok. 6 mm, aby zrównać go z wyświetlaczem 7-segmentowym i górną częścią obudowy. Z podstawki precyzyjnej DIL40 wycinamy listwę 16 pinów, wkładamy w odpowiednie miejsce na płytce i przykręcamy wyświetlacz LCD śrubami z użyciem tulejek dystansowych. Teraz potrzebujemy pręcików, które przylutujemy do płytki LCD i wbijemy w listwę. Świetnie nadają się tutaj pręty pozyskane z listwy goldpinów o rastrze 2 mm - te z 2,54 mm są za grube. Wkładamy po kolei wszystkie 16 kołków, wbijamy w listwę i lutujemy do wyświetlacza. Teraz listwa powinna być sztywno w płytce, ułatwiając nam wygodne przylutowanie jej. Przy tych czynnościach polecam zostawić folię na LCD lub zastosować dodatkowe zabezpieczenie, ponieważ ekran zostanie opryskany topnikiem.
Wyświetlacze są demontowalne, a to szczególnie ważne w przypadku LCD, bo pod nim znajdzie się wkręt mocujący do obudowy. Polecam zastosowanie LCD z białym tekstem i czarnym tłem - pasuje do koloru obudowy i jest dobrze czytelny przy silnym oświetleniu zewnętrznym.
Teraz musimy połączyć masy w J1 i pogrubić ścieżki zasilania oraz obwodów wyjściowych (te niepokryte soldermaską), przez które będą płynąć duże prądy - najlepiej przylutować grube druty i zalać cyną. Kondensator elektrolityczny C1 lutujemy poziomo, a zanim zamontujemy tranzystor MOSFET Q8, musimy wcześniej zamontować potencjometr R56. Trzeba wziąć odpowiedni zapas wysokości nóżek tranzystora, który zostanie wygięty poziomo (po kalibracji R56). Zostały nam do lutowania przyciski, diody i impulsator. Polecam zastosowanie diody LED o średnicy 3 mm z płaskim czołem, które lutujemy przez tuleje dystansowe o wysokości 11...12 mm. Jako przyciski zastosowałem popularne mikroswitche 13,5 mm po wsunięciu pod nie laminatu o grubości 1,5 mm. Impulsator o wysokości osi 25 mm pasuje idealnie - lutujemy go typowo. Potencjometrze kontrastu montujemy w lewym górnym rogu.
Teraz można zaprogramować mikrokontroler - odpowiednie pady umieszczono na spodzie płytki drukowanej. Oprogramowanie zajmuje prawie całą pamięć Flash (92%) mikrokontrolera. Oprócz wgrania programu, musimy zmienić niektóre ustawienia fuse-bit: wyłączyć JTAG, jako źródło taktowania wskazać zewnętrzny kwarc o dużej częstotliwości, włączyć Brown-Out Detector (4,0 V). Wprawdzie zastosowaliśmy zewnętrzny układ zerujący DS1813-10, ale na wszelki wypadek warto jeszcze włączyć BOD, aby chronić zawartość pamięci EEPROM. Po zaprogramowaniu, urządzenie powinno "ożyć". Ustawiamy kontrast LCD potencjometrem R18. Usuwamy przewody programowania i lutujemy brakujący rezystor- zworę R41.
Teraz przechodzimy do kalibrowania bloku pomiaru prądu. Ustawiamy impulatorem maksymalne obroty, przez co tranzystor wyjściowy będzie stale otwarty. Do wyjścia dołączamy obciążenie (np. rezystor mocy) szeregowo z amperomierzem i ustawiamy wartość prądu np. 2 A. Wprawdzie zakres pomiarowy to aż 3,5 A, ale nie zalecam pracy z takimi prądami (robi się gorąco), poza tym kalibrację warto przeprowadzić na niższych prądach (podobnych do tych w normalnej pracy), ponieważ przetwornik w ATmega16A ma zauważalną nieliniowością.
Prąd rezystorów można doregulować, zmieniając napięcie zasilania. Ustawiamy potencjometr R56 w takiej pozycji, aby zrównać wskazanie na LCD ze wskazaniem amperomierza. Kiedy to zrobimy, wyłączamy zasilanie, czekamy aż sterownik ostygnie i zabezpieczamy potencjometr przed rozregulowaniem się, ja upuściłem na niego kroplę lakieru do paznokci, a kiedy wysechł, wygiąłem tranzystor mocy Q8, aby zmieścił się w obudowie.
Kiedy elektronika jest gotowa, przechodzimy do montażu złączy. Jako gniazdo zasilania warto zastosować DC-jack 5,5/2,1 mm, a na wyjściu jack-5,5/2,5 mm, co uniemożliwi pomyłkowe przyłączenie zasilacza do wyjścia. Gniazdo przycisku nożnego to jack stereo 6,3 mm z wyłącznikami, przykręcane do panelu. Ważne, aby miał krótkie wyprowadzenia, bo jest mało miejsca.
Te trzy gniazda mocujemy na prawym panelu bocznym obudowy. Na panelu prawym montujemy tylko wyjście źródła prądowego - zastosowałem najmniejszego jacka mono (czyli 2,5 mm). Montaż gniazd należy wykonać precyzyjnie i starannie. Dolna część obudowy ma na dwóch przeciwległych rogach pręty, na które nakładamy PCB, a na pozostałych rogach montujemy dwie śruby trzymające obudowę. Zmontowaną płytkę drukowaną pokazano na fotografiach 3...5, które mogą być pomocne podczas montażu.
W dolnej części obudowy należy wykonać dwie przeróbki. Po pierwsze, trzeba ściąć jedną z czterech tulejek na wkręty, tę nachodzącą na gniazdo jack 6,3 mm (pozostałe posłużą do przykręcenia płytki). Po drugie, wywiercić dwa otwory na wspomniane wcześniej śruby M3 mocujące obudowę.
Modyfikacje górnej części obudowy są już bardziej wymagające, bo trzeba zrobić w niej wycięcia na wyświetlacze, przyciski, diody, impulsator i śruby. Aby tą czynność ułatwić sobie i Czytelnikom, przygotowałem w projekcie EAGLE warstwę zawierającą kontury, która po wydrukowaniu w skali 1:1, ułatwi wycentrowanie kartki na obudowie i wykonanie cięć i otworów w odpowiednich miejscach.
Wygenerowałem ją również w formacie PDF, w odbiciu lustrzanym. Na fotografii 6 możemy zobaczyć gotową górną pokrywę oraz elektronikę zainstalowaną już w części dolnej, wraz z panelami bocznymi i przykręconymi wyświetlaczami.
Kiedy wszystko jest na swoim miejscu, zamykamy obudowę. Skręcamy ją dwiema śrubami M3 po przekątnej. Od spodu przyklejamy kwadratowe, silikonowe nóżki gumowe. Na oś impulsatora należy nałożyć gałkę. Warto też zrobić coś, aby zabezpieczyć urządzenie przed wpadaniem pyłu i wiórów przez otwory w obudowie.
Obsługa
Obsługę urządzenia podzieliłem na trzy tryby, wskazywane przez diody LED i wybierane przyciskami obok nich. Pierwszy tryb to praca stała z zadanymi obrotami, z możliwością ich skokowej zmiany na inne po naciśnięciu pedału. Zawartość wyświetlacza pokazano na fotografii 7, gdy nie podłączyliśmy pedału (5a) oraz gdy go podłączyliśmy (5b). Należy dodać, że tutaj pedał płynny pracuje w trybie skokowym z zadanym (lub domyślnym) progiem przełączania. Do regulacji obrotów służy impulsator.
Gdy pedał jest naciśnięty, regulacja będzie dotyczyć obrotów właśnie w tym stanie.
Drugi tryb to regulacja płynna. Do tego niezbędny jest odpowiedni pedał, jeśli takiego nie podłączyliśmy, wyświetli się stosowny komunikat, a silnik będzie zatrzymany. Po podłączeniu, zawartość wyświetlacza jest identyczna jak na fotografii 5b i w identyczny sposób zmieniany nastawy. Wartości te dotyczą skrajnych pozycji pedału, pomiędzy którymi przejścia są płynne. Zarówno w tym, jak i poprzednim trybie, nastawy obrotów mogą być dowolne - obroty przy naciskaniu pedału mogą być zwiększane, zmniejszane lub niezmienne.
Tryb trzeci to regulacja obciążeniowa.
Jałowo silnik wiertarki ma wolno się obracać, pozwalając nam dokładnie wycelować wiertłem miejsce do wykonania otworu.
Po dociśnięciu i obciążeniu silnika, pobór prądu znacznie wzrasta, co po przekroczeniu zadanej granicy spowoduje zwiększenie wypełnienia przebiegu zasilającego, zwiększając moc. Po zwolnieniu obciążenia wiertarki, prąd pobierany spada poniżej wartości granicznej i obroty z powrotem są zmniejszane. Jest też możliwość korzystania z pedału w trybie skokowym - jego naciśnięcie ustawia zadane obroty, bez względu na prąd obciążenia. Zawartość wyświetlacza jest pokazana na fotografii 8, kiedy nie nacisnęliśmy pedału (8a) oraz gdy nacisnęliśmy (fot. 8b). Symbole po lewej stronie oznaczają obroty (wypełnienie PWM) odpowiednio bez i z obciążeniem, na po prawej na górze pobierany prąd, a poniżej - zadany prąd graniczny, po przekroczeniu którego zwiększane są obroty. Kręcąc gałką impulsatora zmieniamy obroty jałowe (8a) lub obroty przy naciśniętym przycisku nożnym (fot. 8b).
Aby zmienić prąd graniczny, naciskamy ponownie przycisk tryb 3 (fot. 8c) i zadajemy wartość impulsatorem. Krok regulacji jest zmienny, aby zapewnić szybką i praktyczną obsługę. Naciskając gałkę impulsatora lub ponownie przycisk tryb 3, zmieniamy obroty (wypełnienie PWM) pod obciążeniem (fotografia 6d). Z ustawień można w dowolnym momencie wyjść, wybierając przycisk wstecz. Urządzenie nie pozwala ustawić obrotów pod obciążeniem niższych niż jałowe.
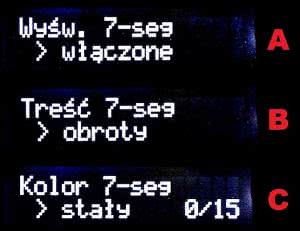
Fotografia 9. Wygląd wyświetlacza głównego podczas ustawiania parametrów wyświetlacza 7-segmentowego
Wybierając przycisk na górze po prawej, wchodzimy w konfigurację wyświetlaczy 7-segmentowych (fotografia 9). Pierwsza opcja to włącz/wyłącz (fot. 9a). Jeśli wybraliśmy włączone, naciskając przycisk ponownie lub gałkę impulsatora, przechodzimy do wyboru treści (fot. 9b). Wyświetlacze mogą pokazywać bieżące obroty (0-15) lub bieżący prąd obciążenia w formacie X,X [A]. Trzecia pozycja tego menu to konfiguracja barwy wyświetlaczy (fot. 9c). Możemy ją uzależnić od bieżących obrotów, prądu obciążenia (płynna zmiana G->R następuje w zakresie 0,2-1,9 A) lub, jeśli miganie kolorami nam przeszkadza, wybrać dowolny kolor stały z palety 0-15, wchodząc i wychodząc z tego podmenu przyciskiem gałki impulsatora. Przyciskiem poniżej poprzednio opisanego, wchodzimy w konfigurację przycisku nożnego, jeśli jest dołączony. W przypadku pedału skokowego, mamy w menu tylko jedną pozycję - wybór jego polaryzacji (NO/ NC), jak na fotografii 10a. Obracając impulsatorem możemy zmieniać to ustawienie, a po naciśnięciu dowolnego przycisku (również gałki) wychodzimy, akceptując zmiany.
W prawym górnym rogu znajduje się ikonka, która ułatwia nam czynność - wskazuje, jak przy obecnej nastawie interpretowana jest pozycja pedału. Naciskając go, ikonka ta będzie się na bieżąco zmieniać. Ta nastawa nie jest zapisywana w pamięci EEPROM, ponieważ polaryzacja pedału skokowego jest rozpoznawana automatycznie po każdorazowym jego podłączeniu, zakładając, że nie był wtedy naciśnięty. W menu konfiguracji pedału płynnego możemy dokonać kalibracji jego zakresu (fot. 10b, fot. 10c) oraz wskazać dogodny dla nas próg podczas pracy w trybie skokowym (fot. 10d). W tej pierwszej pozycji naciskamy pedał do oporu, zwalniamy i wciskamy OK, czyli gałkę impulsatora.
Dwie liczby w dolnym wierszu to wartości zebrane z ADC (FOOT-MEAS) - minimalna i maksymalna. Różnica między nimi musi być odpowiednio duża (>200), kiedy tak będzie, pojawią się dwie ikonki obok tych liczb (8c), wskazujące, która z tych wartości z ADC reprezentuje jako pedał zwolniony, a która naciśnięty. Obecność ikonek oznacza możliwość wprowadzenia nowych danych kalibracji do pamięci EEPROM.
Są one nieco zawężane, aby pewnie pokryć cały zakres. Jednocześnie zapamiętywana jest polaryzacja pedału, dlatego ważne, aby pedał był w tym momencie zwolniony. Druga pozycja w menu (fot. 10d) to ustawienie progu przy pracy skokowej (gdy podłączymy pedał płynny w trybie 1 lub 3). Jeśli chcemy zmienić tylko tą nastawę, nie przechodząc po drodze przez kalibrację, naciskamy wtedy ponownie przycisk konfiguracji pedału. Naciskamy pedał do pozycji, po przekroczeniu której w trybie skokowym ma być traktowany jak wciśnięty i zapamiętujemy nastawę wciskając OK (gałkę). Liczba wskazuje nam wartość na bieżąco zebraną z ADC. Podobnie jak przy kalibracji zakresu, wciśnięcie dowolnego innego przycisku porzuca zmiany. Co więcej, regulacja progu skokowego nie jest w żaden sposób związana ze skalibrowanym zakresem - nic nie stoi na przeszkodzie, aby skalibrować sobie węższy zakres niż pozwala na to zakres ruchu, a potem dowolnie wskazać próg - jak nam wygodnie. Jeśli nie mamy muzycznego pedału ekspresji lub głośności, lutujemy do wtyczki jack potencjometr z zakresu 5...500 kV (ślizgacz na tip) i możemy sprawdzić działanie sterownika. Warto dodać, że po podłączeniu i rozpoznaniu typu pedału, urządzenie oznajmi to mrugnięciem diody - dla skokowego tej od trybu 1, a dla płynnego diodą od trybu 2.
Na koniec
Pamięć EEPROM ma ona dużą, ale jednak ograniczoną liczbę cykli zapisu, dlatego program został napisany w sposób, który nie tylko ją oszczędza, ale także dba o to, aby dane były zapisywane w sposób kolejkowany, kiedy pamięć zasygnalizuje, że jest gotowa na następną daną. Liczby takie jak kalibracja pedału płynnego, ustawienia treści i koloru wyświetlaczy 7-segmentowych oraz prąd graniczny w trybie 3 są zapisywane natychmiast po wyjściu z ustawień.
Natomiast nastawy takie jak zadane obroty, regulowane impulsatorem bez wchodzenia w menu, są zapamiętywane z ok. półtorasekundowym opóźnieniem po zakończeniu ich modyfikacji. Zapobiega to bezsensownemu nadpisywaniu pamięci EEPROM co każdy skok impulsatora. Pamiętajmy o tym podczas eksploatacji, kiedy chcemy nieulotnie zapamiętać nowe nastawy, aby nie wyciągać natychmiast wtyczki zasilania. Programowa obsługa EEPROM znajduje się w przerwaniu Timer0 wywoływanym co ok. 1 ms.
Chcąc zaktualizować zmienną w tej pamięci, w programie ustawiana jest odpowiednia flaga oraz ewentualne opóźnienie. Przerwanie timera najpierw odlicza odpowiednią ilość czasu, a następnie zaczyna sprawdzać flagi. Jeśli trafi na ustawioną, sprawdza, czy pamięć jest gotowa. Jeśli tak, wysyła daną do zapisu, a flagę zeruje. W kolejnym przerwaniu flagi sprawdzane są od nowa. Takie rozwiązanie gwarantuje porządek i bezbłędność aktualizacji danych. Na początku programu, po włączeniu zasilania, sprawdzana jest zawartość pamięci EEPROM, czy dane w niej są poprawne - wówczas jej zawartość jest ładowana do zmiennych w pamięci SRAM. Jeśli nie są poprawne, a ma to miejsce m. in. po zaprogramowaniu mikrokontrolera, kiedy w EEPROMie są same jedynki, zapisywane tam i przyjmowane są wartości domyślne.
W praktyce sterownik sprawdza się bardzo dobrze. Możliwość kontroli silnika przy użyciu stopy znacznie zwiększyła komfort pracy z miniwiertarką, a mnogość trybów i płynnej regulacji pozwala dostosowywać i zmieniać obroty silnika do konkretnego zadania. W połączeniu z punktakiem, można precyzyjnie wykonywać estetyczne otwory w różnych materiałach - jak wiadomo, nie we wszystkim wiercimy na wysokich obrotach (np. w drewnie). Mój sterownik współpracuje z 12-woltową miniwiertarką, kupioną pięć lat temu za 20 złotych.
Używam pedału skokowego, zrobionego z uniwersalnego przycisku nożnego. Kwestię wykonania LED lampki doświetlającej, zasilanej z wbudowanego źródła 15 mA, pozostawiam Czytelnikom. Jak wspomniałem, sumaryczne napięcie przewodzenia szeregu diod nie powinno przekraczać napięcia zasilania minus 1,5 V.
Michał Pędzimąż
mpedzimaz@gmail.com